In today’s rapidly evolving tech landscape, digital twin technology is making waves, transforming industries with its virtual innovation. Imagine having a virtual replica of a physical object that allows you to test scenarios and predict outcomes without real-world consequences. Sounds like science fiction, right? Well, this futuristic concept is here and revolutionizing how industries operate. This blog post explores digital twin technology, its impact on various sectors, and why tech enthusiasts, industry professionals, and innovators should pay close attention.
Digital Twin Technology Innovation
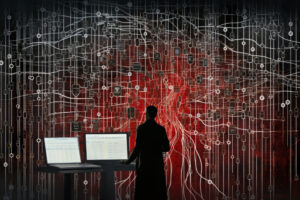
Okay, so let’s dive a little deeper into the nitty-gritty of how digital twin technology is shaking things up! Picture this: you’re in the automotive industry, and with digital twins, you can simulate the performance of a car model before it’s even built. Talk about a game-changer! This isn’t just about testing, though. It’s about innovating faster and smarter. By creating virtual replicas, companies can experiment with new materials, designs, and features without the hefty price tag of physical prototypes. But wait, there’s more! Industries like healthcare are also jumping onboard, using digital twins to simulate patient-specifically tailored treatments, leading to more personalized healthcare. It’s like having a crystal ball, only fuelled by data and tech magic!
The Rise of Digital Twin Technology
With Industry 4.0 continuing to evolve, the rise of digital twin technology has been nothing short of meteoric. Originating as an innovative tool to improve manufacturing processes, it has expanded across multiple sectors. According to a recent study by Gartner, the digital twin market is expected to grow by 38% annually, reaching $48.2 billion by 2026. This explosive growth is fuelled by its capability to enhance performance, reduce costs, and drive innovation.
Digital twin technology creates a dynamic software model of a physical system, allowing for real-time monitoring and optimization. This virtual representation provides insights that were previously unimaginable, enabling companies to make informed decisions quickly. Tech giants like IBM and Microsoft are at the forefront, investing heavily in this technology to gain a competitive edge.
But what exactly makes digital twins so appealing? It all boils down to their ability to simulate real-world conditions, offering unprecedented levels of control and foresight. From predicting machine failures to optimizing production lines, the applications are virtually limitless. The allure of digital twin technology lies in its potential to reshape industries as diverse as healthcare, automotive, and energy.
Unravelling the Mechanics of Virtual Innovation
At its core, digital twin technology merges several advanced technologies, including IoT, AI, and big data analytics. The process starts with the collection of data from sensors embedded in physical assets. This information is then fed into a virtual model, creating a digital twin that mirrors its real-world counterpart.
One key advantage of digital twins is their ability to enable predictive maintenance. By continuously analysing data streams, these virtual models can identify anomalies and forecast when equipment might fail. GE Aviation, for example, uses digital twins to monitor the health of its aircraft engines. This proactive approach reduces downtime significantly and ensures passenger safety.
The beauty of digital twin technology lies in its versatility. It can be tailored to suit different industries and applications. In the manufacturing sector, digital twins can simulate production processes, optimizing efficiency and minimizing waste. Meanwhile, in healthcare, they offer insights into patient-specific treatment plans, revolutionizing personalized medicine.
Industry 4.0 Meets Digital Twins
Industry 4.0 represents the fusion of advanced technologies, driving the development of smart factories and interconnected systems. Digital twin technology plays a pivotal role in this transformation. By creating virtual replicas of entire production environments, companies can test and refine new processes before implementing them.
Siemens, a leader in industrial automation, leverages digital twins to optimize manufacturing operations. Their virtual models allow for real-time monitoring and analysis of production lines, resulting in improved output and reduced costs. This level of precision and foresight has become a game-changer for manufacturers looking to stay competitive in a rapidly changing landscape.
The automotive industry is also reaping the benefits of digital twin technology. With the rise of electric and autonomous vehicles, car manufacturers are under pressure to innovate. By simulating vehicle performance and testing new features virtually, companies can accelerate product development cycles and bring cutting-edge technologies to market faster.
The Healthcare Revolution
Healthcare is on the brink of a revolution, driven by digital twin technology. Imagine a world where doctors can create virtual models of patients, allowing for personalized treatment plans and better outcomes. This concept is no longer confined to the realm of science fiction; it’s becoming a reality in hospitals and research centres worldwide.
By harnessing patient data and creating digital twins, healthcare professionals can gain insights into disease progression and predict treatment responses. This level of precision medicine is transforming how conditions such as cancer and heart disease are managed. It’s not just about treating symptoms; it’s about understanding the underlying causes and tailoring interventions accordingly.
The potential applications are vast, from simulating surgical procedures to improving drug development. Researchers are exploring how digital twins can optimize clinical trials, reducing the time and cost associated with bringing new therapies to market. This innovation represents a paradigm shift in healthcare, with the promise of better patient outcomes and more efficient healthcare delivery.
Automotive Innovations on the Fast Track
The automotive industry is undergoing a seismic shift, with digital twin technology at the forefront of this transformation. Car manufacturers are leveraging virtual models to optimize vehicle design, enhance safety features, and accelerate the development of autonomous driving systems.
One notable example is Tesla, which uses digital twins to monitor and update its fleet of electric vehicles remotely. This capability allows for real-time software updates, ensuring optimal performance and addressing potential issues before they arise. The ability to simulate driving conditions and test new features virtually is revolutionizing how cars are developed and maintained.
Digital twins are also playing a crucial role in the development of connected and autonomous vehicles. By creating virtual replicas of entire traffic systems, engineers can test and refine algorithms, ensuring safe and efficient navigation. This technology is paving the way for a future where self-driving cars are a common sight on our roads.
The Energy Sector’s Digital Transformation
In the energy sector, digital twin technology is driving innovation and sustainability. By creating virtual models of power plants and renewable energy installations, companies can optimize operations and reduce environmental impact.
For instance, wind farm operators use digital twins to monitor turbine performance and predict maintenance needs. This proactive approach maximizes energy output and minimizes downtime, resulting in increased efficiency and reduced costs. The ability to simulate weather conditions and assess the impact on energy production is a significant advantage in an industry heavily influenced by environmental factors.
Digital twins are also transforming the oil and gas sector, enabling companies to optimize extraction processes and improve safety. By creating virtual models of offshore platforms, engineers can simulate various scenarios, identifying potential risks and optimizing operations.
A Deep Dive into Predictive Maintenance
Predictive maintenance is one of the most impactful applications of digital twin technology. By analysing data from sensors embedded in machinery, digital twins can identify patterns and anomalies, predicting when equipment is likely to fail. This proactive approach reduces downtime, extends the lifespan of assets, and minimizes maintenance costs.
GE Aviation is a prime example An error occurred during generation. Please try again or contact support if it continues.
If you’re interested in diving deeper into the role of digital twin technology in the energy sector, there are numerous resources available online to explore. The Innovation Blog by Siemens offers insightful articles on how digital twins are evolving across various industries. For those keen on learning about predictive maintenance, IBM’s Industry Solutions page provides a comprehensive overview of its applications and benefits. Additionally, reviewing GE Aviation’s perspective on digital automation gives a glimpse into the practical applications and future potential within aerospace engineering. These resources can provide valuable knowledge and further understanding of how digital twins are shaping the future.
To explore more about the intersection of technology and business strategies, consider visiting FitBizHouse’s Business Category. This resource offers a lively mix of articles that delve into the latest trends, insightful strategies, and innovative solutions driving modern business success. Whether you’re an entrepreneur or a tech enthusiast, you’ll find engaging content that bridges the gap between cutting-edge technology and practical business applications.
digital twins, energy sector, renewable energy, optimization, predictive maintenance, virtual models, efficiency, cost reduction, innovation, sensor data, industry transformation